数控切割机电极丝的校正,在数控切割机制作中,电极丝相较于工件相对位置的精确性是相当重要的,因为电极丝的定位位置就是制作程序的肇始位置,所以整个切割图形相较于模具件的位置准确性完全决定于电极丝的严格定位。下面随上海率原机电来详细了解一下数控切割机电极丝的校正等相关问题。
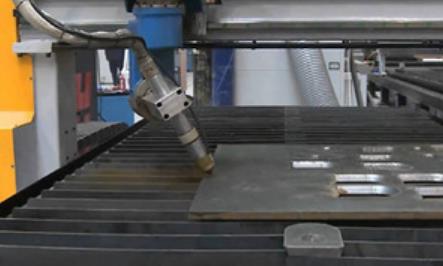
正式加工前,必需对电极丝进行严格定位。电极丝位置的经常用调整办法有以下几种:目测法对于制作要求比较低的工件,在明确电极丝与工件上相关基准间的相对位置时,可以直观运用目测或借助2^-8倍的放大镜来进行留意。数控切割机运用穿丝孔处划出的十字墓准线,分别沿划线方向留意电极丝与基准线的相对位置,根据二者的偏离状况移动操作台,当电极丝中心分别与纵横方向基准线重合时.操作台纵、横方向上的读数就明确了电极丝中心的位置。
移动操作台使工件的基准面渐渐靠近电极丝,当数控切割机一开始出现电火苗时,记下操作台的相对应坐标值,而后根据放电间隔的大小即可测算出电极丝中心的目前坐标值.此法经过电极丝与工件间的火苗产生来测算电极丝的坐标位置,会因电极丝靠近垂准面时产生的放电间隔,与正常制作切割情况下的放电间陈不完全一致而产生定位误差。自动找中心自动找中心法,就是让电极丝在工件内孔的中心位自动进行定位。此法就是根据线电极与工件间发生的短路信号来明确电极丝的目前位置,并由此自动求出孔的中心位置。习惯上或者称为短路法。
首先关掉机床的脉冲电源方向上慢速移动并与孔壁接触,而后运用数控切割机数控系统的半程移动指令G82,让线电极在X轴,系统发出了短路信号后自动返回到孔中心位置,接着在另一轴的方向进行上面说的全过程,这么一个双向移动全过程后,可以使电极丝自动定位到两次移动的中心位置。
数控切割机实际制作程序中,电极丝移动进给路径的编制普通是直观根据零配件的制作轮脚尺寸来布置制作进给路线的,这样会使编程非常方便。若是数控切割机数控系统不具有间隔补给偏移功能,为了让电极丝的中心运动在所需要制作的轮廓线的一边电极丝的半径位置处,就需要根据工件形状大小及电极丝直径和放电间隔计算出电极丝中心点所在的坐标位置,这需要进行大皿的额外计算,并且,每一次调换不一样直径的电极丝和运用不一样的电规准,都要从头进行每个坐标点的计算,给编程和制作都带来巨大的麻烦。运用间隔补给功能后,电极丝的移动路线完全依据实际工件轮廓来编程,并且舀模、凹模、卸料板、固定板等成套模具零配件只需按工件尺寸编制出一套制作程序,只须运用不一样的补给值,即可符合制作的需求,这样大大地简化了制作程序的编制和计算。
为了减小数控切割机制作编程的工作量,当前己普遍运用带有间隔自动补给功能的数控系统。这种数控系统的运算和控制功能要比旧系统强大得多,它经过4B格式的制作程序,能在编程路径的基础上,使电极丝相较于编程图样自动地向工件轮廓的外或内偏移一个提早设定的补给值。运用这一功能,省去了大最的偏移坐标计算,同时也妥兽解决了不一样直径的电极丝的运用调换和不一样放电间隔对制作精度的影响。另一方面对于同一套模具上的凹模、凸模和固定板、卸料板等零配件,只须编制一个进给路径移动程序,便可经过修改间批改量的大小和偏移方向。